Taking the road less travelled
April 2, 2021
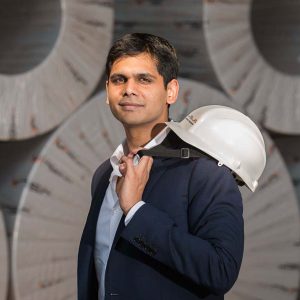
Paving way for environmentally sustainable practices in the metal manufacturing sector
I was intrigued by the sheer quantum of Environmental Clearance documents while reviewing the project for capacity expansion at our Jajpur facility in the state of Odisha. The volume of the terms and conditions detailed in that document is indicative of the environmental scrutiny that the metal manufacturing industry is subjected to across the globe. This is an outcome of increased global awareness on environmental risks and the pressing need for switching to sustainable manufacturing systems. Today’s manufacturing industry needs to transform and align with a whole new manufacturing paradigm, geared to meet the needs of Greta Thunberg and her generation. The long-term impacts of environmental damage in the form of climate change, soil erosion, scarcity of resources, and poor air & water quality, have led to deterioration in the quality of human life, and reversal will take a long time even with extensive corrective action.
Environment protection is no longer a ‘wow’ factor that certain corporates focus on; it is the need of the hour to secure our future and leave behind a healthy legacy. The manufacturing industry, without any question, must adopt sustainability as an integral business philosophy across all aspects of manufacturing, be it processes, machines, or systems. In our industry, energy cost accounts for a large share of the cost of production. Nearly one-third of the cost of conversion can be ascribed to energy, which further enunciates the need to switch to greener and more economical sources of energy.
I set upon the drive for sustainable production years ago, when I took charge of the business. I realized that it will not be ‘business as usual’ in the future, considering the severity of the environmental crisis. I had set an organizational target to reduce carbon emissions by 8-10% by 2025. With this goal, our manufacturing facilities began migrating to an eco-efficient and green manufacturing set-up to drastically curb pollution. Green manufacturing has been sewn into the cultural fabric of our workforce. With ‘reduce, re-use, recycle’ as our motto at Jindal Stainless, we have seen some positive developments in the fields of energy, waste, and material management over a period of time.
SMALL STEPS, BIG IMPACT
I firmly believe that no step is small if it is in the right direction. Over the years, we undertook several small in-house initiatives to optimise our energy efficiency. Our engineers succeeded in process automation and optimization across several production processes.
Interventions at Hisar, Haryana Facility
We undertook several measures for energy efficiency optimization as part of our sustainability measures. Our Hisar facility implemented 91 energy conservation projects during 2017-20, which resulted in power savings of 26.39 million kWh and thermal savings of 11561.1 Mkcal. In a short span of three years, we were able to optimize our energy consumption by 4.3%. We reduced our electricity consumption by ~4% and thermal energy consumption by ~2%. In the year 2019-20, the Hisar facility diversified the energy-type mix, to reduce consumption of traditional fuels, leading to the following split: Electricity 46%; Propane 31%; Low Sulphur Heavy Stock 13%; Light Diesel Oil 9%; and Renewable Energy 1%. Our Hisar facility’s Specific Energy Consumption (SEC) of finished products measured in GJ/ton is at par with international stainless steel producers. The SEC of finished products at Hisar now stands at 8.84 GJ/ton, as compared to 12.8 and 9.80 of two leading international stainless steel producers, respectively.
In-house steps undertaken by our team to reduce our energy usage include descaling process to reduce booster pump power consumption; utilization of flue gas heat to raise the temperature of purging gas in the dryer instead of the electrical heater; and reduction in heat loss by revamping the walking beam furnace. Over and above this, energy saving by arresting of air-leakage in the hot rolling section and optimisation of pressure; optimising the running speed of the Melting Shop’s EAF and AOD ID fan by operating it through an AC drive in place of fluid coupling-based Direct On Line starter; optimisation of various fans and pumps by providing Variable Frequency Drive; replacement of conventional lights with LED lights across the facility; hot air dryer system’s replacement with air knife system at PTF to reduce steam and power; and minimizing heat-loss by improving thermal insulation were carried out across various processes.
The Indian government’s Performance Achieve and Trade (PAT) scheme was introduced to achieve an overall energy consumption reduction in energy-intensive industries. The reduction in the specific power consumption (energy per tonne of product) during the PAT Cycle – 2 was 6.3% in 2020, showing a significant improvement over the last few years. Our Hisar facility achieved a reduction of 6% energy consumption in a short period of two years.
Our Hisar facility adopted ISO 50001:2018 energy management standards and we were able to save 1350 tonnes of oil-equivalent per annum of fuel oil by adopting these measures. We also plan to reduce the use of conventional fossil fuels and re-align our water system to optimize rainwater harvesting. We are targeting to increase our share of environment-friendly biofuel consumption by another 3% in the total thermal energy consumption in the next 1-2 years, along with the installation of an additional 200 kWp rooftop solar power plant. This switch to alternative resources will further mitigate 3,850 tons of carbon-di-oxide.
Our commitment towards a sustainable and green environment is testified by the ISO 14001 certification. Through its implementation, we demonstrate the intent of being a better corporate citizen, reduce wastage, ensure appropriate utilization of resources, and improve our carbon footprint. To meet our energy conservation and environmental impact reduction goals, we have set aside a budget for the installation of renewable energy sources. To enhance the green cover, we have undertaken mass plantation programs in and around the facility, and have planted over 1.2 lakh trees.
Interventions at Jajpur, Odisha Facility
Jindal Stainless’ Jajpur facility is a modern and world-class stainless steel production complex. Our state-of-the-art setup perfectly complements our efforts for green manufacturing. Here, we modified a few mills for reduction in SEC; replaced conventional Pneumatic Actuators; improved efficiency of the regenerative feed-water cycle; optimised waste heat recovery from ferro-alloys flue gas; reduced energy consumption by interlocking pollution control equipment with feeding equipment, and optimised utilisation and monitoring of actual load v/s allocated power v/s inadvertent power; controlled the speed of fume exhaust fan & coolant systems; re-utilized waste heat recovery from HAPL & CAPL furnaces; ensured energy-saving through compressed air networking, and plant-wide LED replacement for both indoor and outdoor usage.
These modifications resulted in a reduction in SEC & increased throughput of the mill, resulting in annual energy savings of 32, 89,766 kWh in the last calendar year. We have been consistently improving these numbers by ~8-10% every year. As a result of our efforts, the facility conforms to the Energy Management System of ISO 50001:2018.
Besides, Jindal Stainless made substantial efforts in the last six years towards 100% fly ash utilisation by way of supplying fly ash to brick manufacturing units, asbestos manufacturing plants, and cement plants. Further, bottom ash is supplied for road construction as well as sent to other land development sites as per government guidelines.
To expand green cover, we undertook plantation of more than 3.4 lakh trees covering an area of 193.62 Ha. (38.7% of the total plant area). More than 1.39 lakh trees were further planted in areas near our manufacturing facility under avenue plantation. We also distributed 95,000 free saplings to local villagers to encourage tree plantation. Additionally, we’ve been carrying out green audits by third parties to get a fair evaluation of our efforts on a consistent basis.
Green manufacturing is assuming even more importance with the worsening scarcity of fossil sources and ever–increasing energy prices. The political uncertainty in resource–rich countries has the developing world worried about energy security. For quite some time now, we have aligned our sustainable interventions in line with changing geopolitics. By now, we’ve deployed efficient motors and lighting solutions at both our facilities, spearheaded automation of systems, and adopted smart energy monitoring systems. In terms of the use of renewable energy, we have a 0.68 MW installed solar PV system which we plan to enhance to 2 MW. This will be equivalent to 2% of the total consumption of our Hisar facility. Over and above this, we will purchase solar power from a third party and reduce our consumption from traditional energy sources. We are currently at 1% in terms of the use of biofuels, which will be increased to 5% in the next 3 years. We are taking active steps towards a zero liquid discharge goal as well.
POLICY INTERVENTIONS TO ACCELERATE CHANGE
As a highly capital-intensive industry, ours is a sector that is usually highly leveraged. This leads to restriction in cash flows, thereby leaving little room for investments into decarburization efforts. This is a big barrier towards migrating to green manufacturing. The Indian government must take a holistic approach by removing blockages and incentivizing green manufacturing.
On the policy front, Indian manufacturers expect the next big wave to be triggered by the government, in collaboration with the industry, for hydrogen as a fuel substitute to carbon, along with a focus on the shift to renewables in the stainless and steel industry. Decarburization alternatives supported by incentives by the government to switch to greener fuels will provide the necessary push, since these efforts would require capital investments.
The domestic industry is open to international collaboration for technology and innovation. Large R&D programs, most notably the HIsarna process in Europe, along with other programs in the US and Japan, have delivered several technologies which have the potential to be introduced into the Indian stainless steel sector. These will be game-changers for the Indian industry and a major driver for the push to zero-carbon steel in the long-term.
India is also a signatory to the Paris Declaration (COP 21) which intends to reduce the emission intensity of its GDP by 33-35% by 2030 from 2005 levels. The government has already submitted the Intended Nationally Determined Contributions (INDC) for reducing GHG emissions in iron & steel sector projects. I am confident that with the recently introduced steel scrap and end-of-life vehicle policy by the government, circular economy will pickup and reduce stress on natural resources, along with the increased availability of scrap in the local markets. Any increase in the amount of scrap usage will help in limiting the energy used in making steel.
I believe that the new paradigm of competitiveness will be based upon sustainability, and profitably may get linked to how greenly the business functions. We have mandated our team to migrate to sustainable energy sources with complete in-house solid waste management and zero discharge. More than any target, we are committed to shouldering our share of the responsibility towards our planet. I believe that these targets should be self-imposed rather than waiting for any regulatory compulsion, because sustainability is no more a choice for any business. In the next few years, I aim to make Jindal Stainless’ name synonymous with sustainability, at par with the metal we produce.