Mr Sushim Banerjee
July 25, 2024
Today we are in Kolkata, also known as the cultural capital of India. We are here to interact with the CEO of the Indian Iron and Steel Sector Skill Council, Mr Sushil Banerjee. With his extensive experience in the iron and steel industry, Mr Banerjee has been instrumental in promoting the use of steel and stainless steel in India. Currently, he is involved in the upscaling and scaling of professionals in the iron and steel industry. Let’s see what he has to say about the increasing use of stainless steel in India and also about the initiatives that his organisation is undertaking in order to fill the skill gap in the industry. Dive into this conversation between Supriya Sundriyal from Corporate Communications and Mr Sushim Banerjee.
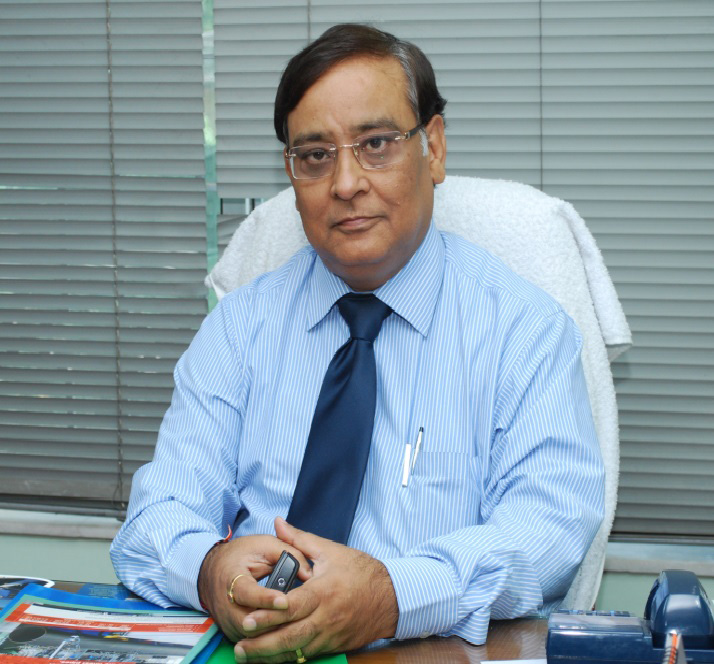
CEO, IISSSC
Please tell us about yourself.
I was born in Calcutta. My father, who was in the teaching profession had a transferable service in various government colleges. So, we moved around from Calcutta to various places in the North Bengal and West Bengal in various locations. My schooling was in Hooghly as well as in Calcutta. And I passed out of Higher Secondary and then was admitted to Presidency College in the subject of Economics. And my father also became a professor of History at Presidency College. So I graduated from Presidency College and studied MA in Economics at Calcutta University. And I’m still proud to say that I stood first in Economics and won the gold medal. And then for some time, I was thinking whether to join the teaching profession, but that time the SAIL exam came and I sat for the exam and was selected in SAIL. That was the year when my life changed along with SAIL. I rose to the position of Executive Director, Commercial. I was also the Executive Director of the Hot Rolling Division (HRD) of SAIL and was the Chief Risk Officer of SAIL. After my stint in SAIL, I was placed as a Director General of the Indian Institute for Steel Development and Growth shortly. Then I became the CEO of the Indian Iron and Steel Sector Skill Council.
Can you elaborate on the work that your organisation is undertaking and its impact on the Iron and Steel industries, especially on the stainless steel industry?
The Indian Iron and Steel Sector Skill Council is one of those Sector Skill Councils out of 37 sector skill councils that the Ministry of Skill Development and Entrepreneurship and also National Skill Development Corporation (NSD) have created. I was associated with the formation of the council way back in 2013. And why we chose Calcutta as the place is because the eastern region is the origin of Indian steel industry. Starting from Burnpur as well as from Tata Steel at Jamshedpur and also various iron ore and coking coal resources at Jharkhand, Odisha, and West Bengal. So, that was the idea of creating this body at Calcutta.
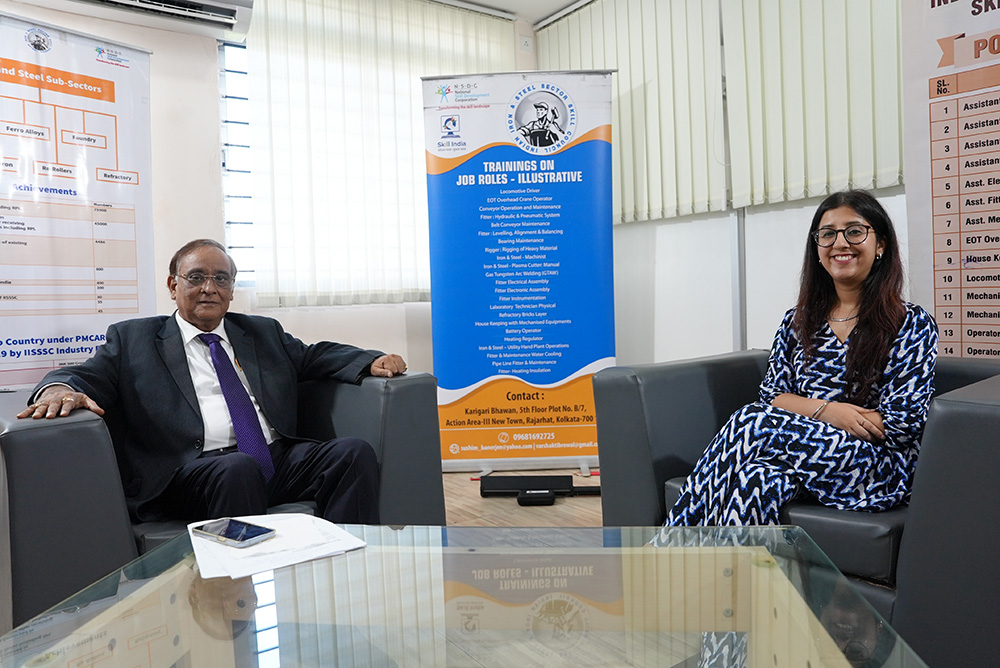
We have done a skill gap study because if you want to do the skill development, it is necessary that you know whatever the skill gap is and where you have to fill that gap. So, the skill gap study was done in detail with the National Institute for Secondary Skill Technology. In the first two years of our formation, we developed the course curricula and contents for all the frontline operations like electricians, welders, machinists, and AOD crane operators, which are the basic operations of running a steel plant. And then after that, after three years, we started training on those courses.
Our training module is a short-term module of three to four months training and we undertake training through our training partners. They have got very experienced trainers under them. So after the training is over, we take the assessment of the people, because we must know how the training was effective in them. So, this learning was through the assessment and the assessment is done by multiple choice questions or face-to-face interviews, and there are various processes. We monitor this assessment and this assessment is done by assessment agencies who are affiliated with us. After the assessment is over, 70% is the benchmark. This skill certificate with a logo of the government is a very valuable document for the candidate. There are three types of areas where we have penetrated – first is the short-term training. The second one is the RPL (recognition of prior learning). There is a huge number of existing labour who is working in the steel plants, but they are just working. They have skill experience, but that skill, what level they are working or what is their skill competency that was never evaluated earlier. So, this is called the recognition of prior learning and this is a short-term module of 16 hours 12 hours of training. So, it is our job to know if there is any skill gap. They have to fill that skill gap. Our trainer is very experienced and then after the training is over after 12 hours, they are being assessed and this certification is taken place. Now, all these things are through a portal. None of these is through any manual manoeuvring. It is all through a portal that is called the Skill India Digital Hub (SIDH). So, anywhere sitting in India, any place you can see how many people were trained, how their performance was, what the level is, we call it as NSQF (National Skill Qualification Framework) – that is the level which will judge their competency level. Level one is unskilled, level eight is fully skilled, it is the MD level. The last one is the apprenticeship. Each unit having an employee of more than 15, they are supposed to have an apprentices. So that is how apprenticeship courses are also different. They are slightly longish courses because apprentices are taken for one and a half years to two years. Till date, we have done about a lakh of training. And I’m very happy to say that we were told by the Ministry that placement of those candidates is also your responsibility. And I feel that is the right approach because placement means how effective your training was. But whether that fellow is actually getting the employment that is also our job. So today 60% of our candidates who have been trained by us are engaged in gainful employment.
What are the broad areas that India should work on to bridge this gap in the iron and steel industry?
Our experience is that in the iron and steel sector, although many professionals are working there, but at the working level, there is a huge skill gap, because once the steel plant starts functioning, they require manpower. They require manpower hands on, who will work with the machines at the shop floor. These people earlier what was happening, these people were not undergoing training in that strict sense of the time, maybe the units that are recruiting them, they used to arrange some, post hiring training for a few days’ time. So, those trainings are not very uniform, not any standardised module they are following. So, what this MSD Ministry and NSDC have done that our sector skill council that we have developed those courses and contents, very much what the industry needs. I’m very happy to say that these courses have been developed with the active support and involvement of the industry. So, industry knows what their requirement is. If you develop those courses, and people are getting successful in getting those courses and training and assessment, then they are getting engaged by the end units. So, skill gap persists, there is a 10 lakh of people will be will have to be trained between now and 2030. That means, today, if it is 2023/ 2024 or 2025, in another six years’ time, another eight lakh fifty thousand working level at the front shop floor level, they have to be trained. So, it is a huge task. And we are going ahead with that, I’m happy to say that some of the big industries all of them are with us
When we approached Jindal Stainless, and I’m very happy to say that they were very enthusiastic because a lot of skilling activities are already going on in JSL. JSL has a skill academy also (Stainless Academy). Stainless steel has actually now penetrated into the various areas which was earlier not there. For instance in some of the areas particularly in construction area, earlier stainless steel, we used to say I’m talking of 1980 etc., they are 80% of the stainless steel demand was from the utensil sector. And now there is a sea change, it is now more industry focussed and less on the utensil sector. But there are many small producers who are making stainless steel and they are catering to the needs of the utensil sector. And I’m very happy to see that Jindal Stainless is now really moving up the ladder in the not only for the quality of products, but also by extending their product coverage, both in long and flat products area. So now infrastructure area, they are now targeting and I’m sure this is an area where Jindal Stainless particularly use of stainless steel will go up tremendously in our country in the next few years’ time. I’m sure stainless steel has a very bright future. It is not only because why do we demand stainless steel – people say wherever you require corrosive resistant steel, you use stainless steel, no, it is not only corrosive resistant it is wherever you need good quality steel, stainless steel is an item that is available. Earlier stainless steel long products there were not so many products available, but now TMT bar, round bar, structural, these are available in the stainless steel and that is why the infrastructure sector which uses maximum quantity or major quantity in the long product as well as in flat products. So stainless steel has entered into that infra sector. And now I’m sure it will be very good.
You mentioned that you’ve already trained a lakh people, but is there any vision that you have to target so many people in order to at least bridge some of the skill gap that’s there? Is there any vision, any target that you have in mind?
When the skill gap study was done, they had mentioned about some numbers that these are the number of skill gap. For fresh training, they said it will be about ten lakh in the next decade. So, one lakh in each year and for upskilling and reskilling, for the RPL that is for the existing employees, that target is about eight lakh fifty thousand. That means eighteen lakh fifty thousand people through fresh training as well as through RPL that is our target in the next ten years’ time to achieve, this includes stainless steel also.
What are the new job roles that your organisation can develop based on futuristic processes of manufacturing and what are your views about Jindal Stainless’ Stainless Academy?
I will first say about new job roles for the iron and steel sector that is mostly for the Industry 4.0. So, after much thought and deliberations with the board members and industry, what we have come about that, for the general working level population in the steel plant and for the young officers, young professionals who are working now, it is very necessary that some amount of awareness programme for application of artificial intelligence for application of machine learning, for application of industrial IoT, for application of even PLC, it is very much required. They must be aware of the advantage or benefits of these technologies that are coming. Rather than pushing them that from tomorrow, the whole plant will be run by the artificial intelligence that will be very wrong. The transition has to be gradual so that people understand the benefits and then they themselves will come forward to get them trained. So, that is why we on the advice of National Council of Vocational Education and Training, who approve our job roles, we call it as not only full job role, we call it as micro credentials. This is a focused job role, and the training hours will be starting from seven and a half hours to thirty hours not beyond that, that means two and a half days training will be sufficient in making people aware of the advantage of artificial intelligence in the process they are running. We thought this is the best way to approach a large group of population in the iron and steel sector, which is having some 2.5 million direct and indirect workers working. It is very necessary that they must be fully aware of this advantage of this new technology and then they will themselves will sort of absorb this. So, that is how we are approaching this.
And so far as stainless steel is concerned, I’m very happy to say that Jindal Stainless when we approached them that what are the job roles that you require for your own purpose, they immediately came out that in the downstream area, they require a job role, which can be developed by the council and we thought and they themselves had suggested that heavy fabrication, we call it as the Specialist Heavy Fabrication with Stainless Steel. So, that means stainless steel now current percentage is about 43% of your total sale of stainless steel goes for the architecture, railway and transport and another 27% goes for your automobile, building, and construction. So, these together ABC and ART together takes about 70% of your total consumption of JSL as well as for the total country and balance 30% for the consumer durables or utensils sector. So, you have very rightly approached that these are the industry sector, where we must focus our activities and therefore, for the downstream area for instance in railway now they have decided to make 100% their coaches with stainless steel. So what do you require? You require fabrication you require welding. So, like ROB (road over bridges), there is use of stainless steel. What do you require there? Same. Stainless steel has to be fabricated, stainless steel has to be welded. And these two feature welding is a part of that heavy fabrication course, that is being developed and it has already been done with the active support of JSL.
Once this is done, all your downstream industries, who are involved in fabrication for bridges, for wagons, for ROBs, for flyovers, all these people will be much benefited by this type of training and I’m sure JSL will also be the very much beneficiary of this particular job role. So, that you know JSL product will be used for fabrication of all the infrastructure assets that the country is planning.
This is how we are planning and I’m sure we will have a win-win situation with JSL, their excellent product that will be all be known that will be on be rolled into and fabricated because whatever you may say I have heard you know at least in 100 seminars that when you ask the speaker to list out what are the weakness in Indian Steel industry. First or second point will come there is a lack of fabrication, lack of fabrication facility, lack of good fabricator. We along with JSL want to bridge that gap. We want to make good fabricator with the training of this Specialist Heavy Fabrication where the entry point is B.Tech engineer, they will be the specialists and then of course, they will train all those people who are actually welding, fitting, and fabricating the material.
You’ve been in the industry for so long. How do you think the iron and steel industry has evolved over the years? And how do you think stainless steel fits as the material of choice?
If you look at the total steel industry, let me first talk about the total steel industry, which includes carbon as well as stainless steel, we produced about 144 million tonnes of steel last year in (FY)2024. And we consumed about 136 million tonnes of steel. Ministry of Steel has already brought out the National Steel Policy, which says that by 2030, India will have a capacity of 300 million tonnes. The current capacity of India is 179 million tonnes. So, there is 121 million tonnes gap is there to be built within these seven years, from 2023-24 to 2030-2031. But now, almost all the major producers, they have announced their expansion plan. Even JSL also from 3.2 million to 4.2 million at the expense of some 5,400 crore will be spending in the next three years’ time so that they achieve a capacity of *4.2 million tonnes. So, that is how the industry is growing and the CAGR of Indian consumption today is between 9 to 10%. So, even if the production goes up by 5-6%, it will be achieving that target. But the point is whether the market will be there, because no point in creating capacity without the market. So the market will be there and I’m sure with the main thrust by the government on infra capex, I think there is a massive infrastructure deficit in our country. There are many new sort of railway lines, roads that have to come up so that interconnectivity throughout the country is enhanced. So all these things require steel, whether it is mild steel or stainless steel. Now stainless steel has got their own area, where we require corrosive resistant steel and now there is a good demand for fire resistant steel because in the building sector, there is a good demand for fire resistance that are also being developed here. And the technologies are itself are growing very fast. There is LGSF technology, more and more you are moving there will be light gauge steel with high performance and that is where there is a great scope for stainless steel to pitch in, because it will be a low volume steel, low weight steel, but high performance. And with the high performance, there are duplex variety also you are planning. So, those duplex varieties will satisfy our space research programme. In the space area, they are already using stainless steel in a big way. So, the opportunities, I must say, are abundant. It is not only for the industry, it is all those who are working in the iron and steel industry including the stainless steel.
Stainless steel has a very great future to look up to because now another thing is coming that we are now considering – the lifecycle cost for at least for the all infrastructure assets. The bridge you are making that must survive for another next 100 years. And so, maintenance cost has to be low, how you can achieve that. If you use stainless steel at particular places, they do not require any maintenance. So, for lifecycle analysis, stainless steel has a great role to play. And I’m sure the government will move up with using stainless steel in various applications.
Please elaborate on the growth trajectory of stainless steel in India and in abroad?
There is a great scope for enhancing this production. But then the availability, I believe at 4 MT or 4.5 MT is too low. There is a scope for at least 10 MT of stainless steel availability in our country in the next few years’ time because that is how the demand is growing. And if the demand grows, we cannot depend on just imports. They are not only costly but also kill the domestic incentive to produce. So why should we depend on imports? Last year, some 1.6 MT of stainless steel has been imported. There are about 10 good producers, why not the total demand of the country be met by the indigenous production? That should be the first target. And then as and when there is growth in the market, which I am sure with the way railways are moving, with the way the construction of flyovers, bridges are taking place – there is a great demand that will be emanating. So indigenous production, availability of stainless steel must be enhanced. The stainless steel producer has a great future to play. Only thing is that a lot of awareness campaigns are required.
The use of stainless steel in bridges, coaches is a very recent phenomena. That is why if it goes up, there will be a huge demand for it. We have to create capacities because the market is good but we have to create the market by organising workshops, awareness campaigns throughout the country, particularly in the tier 2 and tier 3 cities.
What advice would you offer to professionals in the iron and steel sector?
First of all, the professionals working in the iron and steel sector, their first duty is to develop a group of young professions who will work and thrive in career in this sector. Because at one time, when steel industry was going through a downward cycle, a lot of people were leaving the industry. But things have changed now. There are good opportunities now available. You must appreciate that a fellow always dreams of a career in an industry that is growing. And that is exactly for the steel industry, it is showing signs of good growth and that good growth is attracting a lot of young professions to this industry.
So all the professions who are already working in this sector, it is their responsibility to bring up, to educate, to train rather than just leaving them to the free whims of the market. Once they do it, young professionals will feel more encouraged and more enthused to continue to work and they will not suddenly leave. If you ask any young professional where you want to join, they will say IT sector or finance, which is now expanding. The iron and steel sector is a very traditional critical industry of the country. Therefore, working in the iron and steel sector today and 15 years ago, there is a sea change now. If you visit any plant, there is much less people working on the shop floor because it is all automated or mechanised. But there are many people working in the process control areas, in the R&C labs, inspection labs, warehousing because these are very critical operations in the iron and steel sector. The iron and steel sector is for metallurgical students only because the students can apply their knowledge in the development of the product and in checking of the product in the R&C lab.
If you are a mechanical engineer, there are a lot of activities in the mechanical area. If you are an electrical engineer, there is a huge electrical dept. Steel industry from mere production is now extending to fabrication, which is a very big phenomena coming now. Industry would like to have good fabricators, good engineer with mechanical background, with structural engineering background. Even structural engineer who can design product, they are very much needed in the steel sector. Even the architectural sector with the knowledge of steel who can design steel product or steel building, they are very much needed because they can the advice the user that you design your house in this fashion.
So this is how the steel plant is branching out in serving the people. You have to capture what people want. You have to know the nuances of the people’s choice. It is not only the nuances of companies but nuances of customers that matter. There, I am sure stainless steel has a great role to play because it is a good product, low-volume product and high performance.
Anything else that I may have missed or you want to add that you’d want our viewers to know about the Iron and Steel industry?
In the Indian Steel Industry, there are two parts. One is the large players who are about 50-55% share of the market and there is SME who have some 45% market. This SME sector has to come forward in a big way in this nation building exercise. They have to skill their people because once your workers are skilled, your productivity goes up, your motivation of people goes up, and you have the instant example of earning more revenues. That is how I would suggest SME of I&S must come forward in skill development, getting their people trained, getting their products certified, getting the whole industry compatible with all the rules and regulations of the country.