Jindal Stainless: Minting Success
July 6, 2022
Back in 1998, Jindal Stainless Hisar received a call from enquiring if Jindal Stainless would be interested in the Minting Business, that is, in producing Coils for the India Government Mint (IGM). Grasping the potential knocking on doors of Jindal Stainless, the present Chairman of Jindal Stainless, Mr Ratan Jindal, along with his colleagues, decided to grab the offer with both hands.
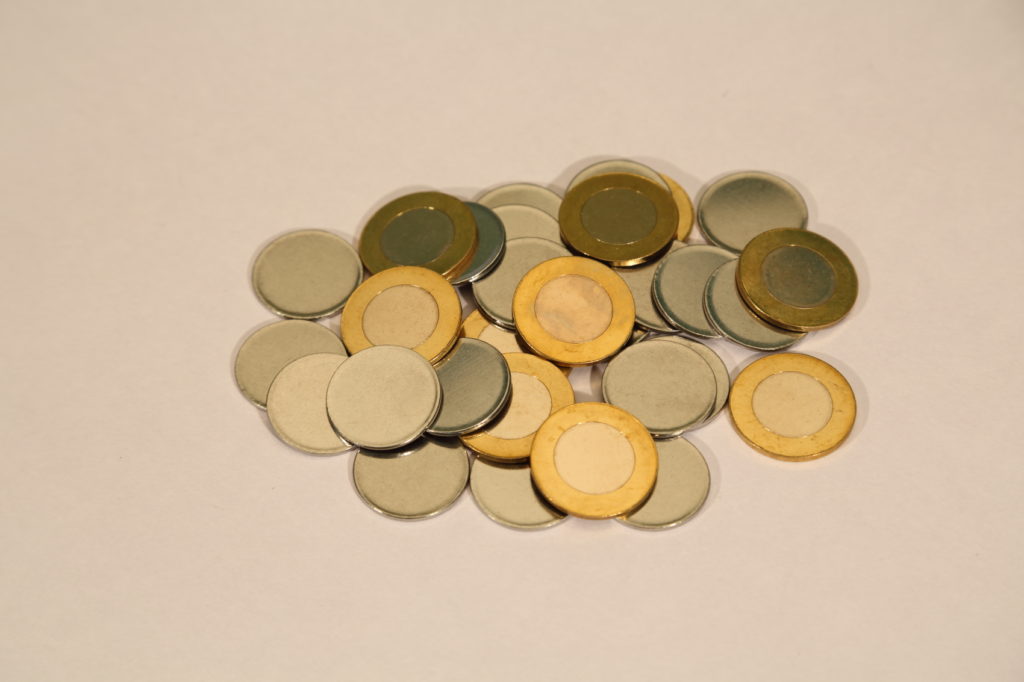
Coins in India: A background
The coins that jingle in our pockets are made with material that emerges as coils from the manufacturing lines. Hence, the business of making coins consists of three crucial steps:
- Manufacturing of coils which is done at the manufacturer facility.
- Punching of coin blanks from the coils which is done at both manufacturer and government facilities.
- Minting of coin blanks which is done only at government facilities to regulate supply of authentic currency in the market.
The Government entity that is responsible for the blanking and minting is India Government Mint (IGM). India has four IGMs at Kolkata, Mumbai, Noida, and Hyderabad. Back in 1998, the IGMs reported into the Ministry of Finance, Government of India. The Reserve Bank of India (RBI) buys coins from the IGM to regulate and standardize banking and the flow of currency in the country. Supplying Coils is referred to as Mint Business and supplying Coin Blanks as Blanking Business, in the industrial phraseology.
Until 1998, Salem Steel Plant, a unit of Steel Authority of India Limited was the only supplier of Coils as well as Coin Blanks to IGMs. Since the demand for steel was rising it was impossible for SAIL to meet the supply constraint situation facing the country. Considering the prevalent circumstances and the trend for future growth, a progressive decision was taken by the government to open the sector for inviting participation from private players. This decision was to change the entire dynamics of coinage in the country, and set in motion a wave of positive changes that continues even today.
Jindal Stainless Enters
The rendezvous of Jindal Stainless with Coin Minting Business began with Shri O.P. Jindal’s vision of ‘Mine to Mint’; a future where Jindal Stainless becomes a major supplier of coils and coin blanks in both the domestic as well as the international market. The phone call marked the beginning of this vision which could only be materialized after the approval from IGM. The process of winning any first time tender with the IGM was arduous and demanding, constituting a few major steps:
- The government officials visit the facility of the manufacturer to inspect their overall manufacturing standards such as quality, safety, inspection etc.
- The above visit includes officials including a group of General Managers of each IGM, as well as a senior level bureaucrat such as Secretary, Ministry of Finance.
- The bidding manufacturer has to comply with a plethora of tender conditions, such as, healthy balance sheet, customer track record, past experience, strict adherence to safety and quality parameters etc.
- If the bidder fulfills the conditions and is able to bag the project at L1 costing (least costing), s/he has to provide pre-production samples to the IGM, for which a maximum of two attempts are granted.
- Only when the manufacturer clears all the above steps, are they accorded consent for commercial production of Coils/ Blanks.
When the opportunity arrived, Jindal Stainless was already producing coils at its Cold and Hot Rolling facilities. Therefore, the Company was able to customize to IGM’s requirement without much process modification. Though there was an initial challenge pertaining to the ‘hardness’ requirement of the Coil, it was addressed swiftly and efficiently by the Hisar Plant leading to the approval by IGM. In the first ever tender for Coils, Jindal Stainless supplied 2,500 metric tonnes (MT) to IGM in 1998. This was just the beginning of a long and glorious journey ahead.
Now that Jindal Stainless had already set foot in one aspect of the Coin Minting Business, it was time to take a significant leap of faith and put the next foot forward. By the turn of the millennium, in the year 2000, Jindal Stainless participated in the bidding for Coin Blanking Business. Since it was the company’s first attempt, a high-level delegation from the Government of India visited the Hisar plant to scrutinize its facilities. Jindal Stainless emerged victorious once again. A humble beginning was made by the Company in supplying 2400 MT of FSS Coin Blanks to IGM of 25 Paisa, 50 Paisa and Rs 1.
Until this point in time, coins in India were largely made out of Ferritic Stainless Steel (FSS) grades, since the currencies in popular use were Re 1 and Rs 2. However, the road that Jindal Stainless had taken in 1998 was about to change its course.
As per Seigniorage Guidelines of the IGM, all coins are mandated to have an intrinsic value of around 60-70 % of its face value. Since stainless steel was a cheaper alternative to some other metals like Copper alloys, coins made of only stainless steel could not meet the required Seigniorage value for higher grade currencies, such as Rs 5 and Rs 10. Therefore, in order to supply material for Rs 5, the intrinsic value of the metal had to be enhanced. Another decision was made by the IGM to introduce Rs 5 in Cupro-Nickel (Cu-Ni) composition, and not FSS.
Jumping on the bandwagon of emerging trends, for the first time in 2001, Jindal Stainless started production of Cu-Ni alloy. The company had to overcome a lot of teething issues in rolling of this product. Eventually, after rigorous Research and Development as well as repeated trials, in the year 2002-03, Jindal Stainless bagged an order of 1,200 MT of Cu-Ni Coils. The order was completed in FY 2003-04. This was a paradigm shift for a company that had no prior experience in producing non-ferrous metals.
Local Coins Go Global
In 2004-05, the Company began foraying in the international coin business. This was the year when Jindal Stainless started supplying FSS Coin Blanks to the French Mint, starting with 700 MT of four different denominations. Led by the then Head of Exports and in collaboration with the French Mint, Jindal Stainless was able to benchmark its products and services in line with stringent international quality parameters in a series of iterative and continuous improvements. The mutually rewarding relationship between Company and Mint continues till date.
Jindal Stainless was climbing up the market ladder and adding more achievements to its bag. 2007 proved to be another crucial year in establishing its global footprint. The Company fulfilled a unique tripartite order for CuNi coins of denomination 1 Thai baht. Under this unique arrangement, the Royal Canadian Mint placed an order for 179 MT of coin blanks on Jindal Stainless. The blanks thus produced were supplied to Noida IGM for Minting. The minted coins were supplied to The Royal Canadian Mint. This one of a kind collaboration among private and government mints of three countries remains a distinctive feat in the Coin Minting Business.
The destiny of the Company took a complete turn when a huge internal shift happened within the government set up in 2007. The separate IGMs were brought together as a corporation, called as Security Printing and Minting Corporation of India (SPMCI). The SPMCI was empowered with a separate Board of Directors, having nominations from disparate Government bodies. This led to promulgation of new purchase policies and guidelines for manufacturers supplying to the IGMs. Since IGMs were no longer directly reporting to the Ministry of Finance, all decisions had to be routed through the SPMCI Board for Ministry approval. Despite the initial challenges to the new ways of doing business with the newly formed SPMCI, Jindal Stainless hit a milestone with its resilience and adaptability. It received an order of whopping 10,000 tons FSS coin blanks from the IGM in 2008-09.
Speed Bumpers along the Way
In 2009, India’s first ever bi-metallic coin was introduced by the India Government Mint and this opened the gates to a magnificent future in bi-metallic Coin Blanking for Jindal Stainless. As the age old saying goes, ‘nothing worth having comes easy’, a crucial hurdle stood between Jindal Stainless and bi-metallic coins. Even though the Company could produce both the ring and the core, there was unavailability of internationally accepted infrastructure to join the two together.
Using this challenge as an opportunity, the Head of Non Ferrous and Coin Blanking along with along with R&D and mechanical teams developed a mechanism for joining the outer ring and the inner core using existing press at Hisar facility. This was such a path-breaking innovation that a group of General Managers from IGM visited the Hisar plant to witness it with their bare eyes. Astounded at the sight that such a feat could be accomplished without the Schuler joining machine, their admiration for the in-house ingenuity exhibited by Hisar team was expressed in the form of approval of the process. Thus, Jindal Stainless obtained its first order of Bi-Metallic Rs 10 Coin Blanks of 1500 MT in FY 2010-11.
The successful completion of the order boosted management’s confidence and the technology for joining blanks was imported from Germany. Two Schuler joining machines were commissioned in 2013 and 2014 respectively. The new technology enhanced the monthly capacity of bimetallic blanks by 300MT with improved quality. Soon the Company got its first bulk order of 3,150 MT. Since then, Jindal Stainless has supplied over 12,000 MT bimetallic Coin Blanks to IGMs.
The ripple effect of the global economic recession of 2008 could be seen on all industries, and stainless was no exemption. Even though the Hisar facility of Jindal Stainless group weathered the storm well, the Jajpur (Odisha) unit of the group, which was in its incipient phase of commissioning and trials, went into the red. This put the financial health of the company under IGM’s radar.
From 2013 to 2015, the Hisar facility was unable to supply Coin Blanks to IGM due to restrictive tender conditions. A subsidiary of the Jindal Stainless (Hisar), Jindal Stainless Steelway Limited (JSSL), took up the mantle to supply to IGMs. The business decision taken out of compulsion way back in 2013 is now a conscious choice for the company. Today, JSSL supplies majority of Coin Blanks to the IGMs. By the year 2015, supplies of FSS by Jindal Stainless peaked to 46,000 MT coils, as Re 1 and Rs 2 coins were growing in vogue till then.
The Road Ahead
As the major supplier of Coin Blanks and Coils to IGMs, Jindal Stainless was poised to rapidly grow its presence in global markets. The Company made direct inroads in international markets. With the currency usage rapidly shifting to plastic currency and digital money, Jindal Stainless is now focused on tying up with the established Mints which supply currency to developing economies, where coins will be in vogue in the near future as well.
Out of nearly 120 Mints in the world, Jindal Stainless is supplying Coin Blanks to the Mints such as French Mint (2005) , Royal Canadian Mint (2007) , Slovak Mint (2011, FSS Coin Blanks), Finland Mint (2017-18), Dutch Mint(2018-19), UK Mint (FY 2021-22), Slovak Mint (FY 2021 for Non Ferrous Coin Blanks). These Mints, in turn, supply coins to developing countries like Bangladesh, Madagascar, Tunisia, Brazil, Guatemala and French Colonies. The aim of Jindal Stainless is to get major shares in export blanks market and unleash the infinite opportunities the field has to offer.
Continuing its journey in bi-metallic coins forward, in May 2021, Jindal Stainless received an order from Slovak Mint for bi-metallic blanks for Dominican Republic and Tunisia. With this order, Jindal Stainless has added another feather in its hat. Till now i.e. Aug’21 Jindal Stainless has produced and supplied over 54,500 MT of Coin Blanks including 12,500 MT of bi-metallic Coin Blanks across the globe..
The India Government Mint introduced Rs.20 bi-metallic coins in 2019. Jindal Stainless was a key contributor in developing Rs.20 coin blanks. Vice President, CRD and SPD, Hisar, recalled an incident when he was shopping in a mall in Delhi and heard a fellow customer appreciating the build and polish of the coin. “I was elated at the man’s appreciation of the coin and told him proudly that Jindal Stainless has a contract with The India Government Mint for the production of Rs. 20 and Rs. 10 coins. It was a moment of revelation for me when I realized that we are doing something that people appreciate.” In January 2020, the Company procured a contract of 2275 MT of Rs 20 bi-metallic and has been a regular and trusted supplier to IGM.
The SPMCI is also innovating along with the manufacturers to improve the aesthetics of the coins and to increase their adoption and usage by the general public. Taking the endeavour forward, Jindal Stainless has developed Tri-Metallic Coin Blanks for Rs 50 currency, and is awaiting approval on this project.
Ticket to Success
Throughout this journey, the one enduring reason that has helped Jindal Stainless become one of the world’s leading suppliers of coin blanks is adaptability. The Company has not just been flexible, but proactive, in responding to change; from change of technology, process, products, people, and to everything else. As recently as India’s Independence Day 2021, the Coin Blanking unit developed customized medals for distribution among prize-winning employees.
In uncertain times such as this pandemic, companies need to rethink and re-strategize to keep their businesses running and to do that they have to adapt to the present circumstances. Tapping into reserves and using that to innovate and collaborate with other players in the market is the key to maintain resilience. Jindal Stainless has proved its resilience and adaptability with diversifying its product portfolio across the years with each emerging opportunity and by collaborating with various Mints all over the world to expand its export business.
Since two in every five coins in the world is made with material produced by Jindal Stainless, it’s very unlikely that the reader hasn’t held this journey of success in the palm of their hands and heard it jingling a Swadeshi rhythm in their pockets. The feeling of travelling to another country and holding a coin of another currency in your hand that Jindal Stainless has produced will continue to make Indians proud.